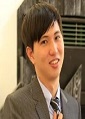
Yen-Ting Chen
National Cheng Kung University, Taiwan
Title: Effect of process parameters on dimension of single-track ss316l deposited by direct energy deposition
Biography
Biography: Yen-Ting Chen
Abstract
Direct Energy Deposition (DED) has been recently applied for production of complex structure and for different areas, because of its convenient feature. However, there are still lots of problems, such as how to control the process parameters to get demand cladding dimension and to improve product properties. The purpose of this research is to analyze the effect of process parameters on a dimension of single-track 316L stainless steel by DED and find a prediction index of dimension control. In this study, DED experiments were carried out with powder and substrate of 316L stainless steel to investigate the influences of process parameters (Laser Power and Scan speed) on laser forming properties. Software ImageJ was used to analyze the dimensions and morphology. From our results, it was found that an increase in laser power leads to increasing the cladding area, height, and width. Secondly, an increase in scan speed results in the un-symmetric morphology of cladding, and in decreasing the area and height of cladding, but it doesn’t have the significant influence on the cladding width. Thirdly, energy index and dimension index could be used to help with controlling process parameters. When the energy index E*>50, molten pool boundary expands across to the substrate and make it could be always found in the re-melt zone below the substrate. For dimension index DI > 0.8, more powder could be deposited on the substrate (cross-section area of per unit track is larger than 1.8mm2).